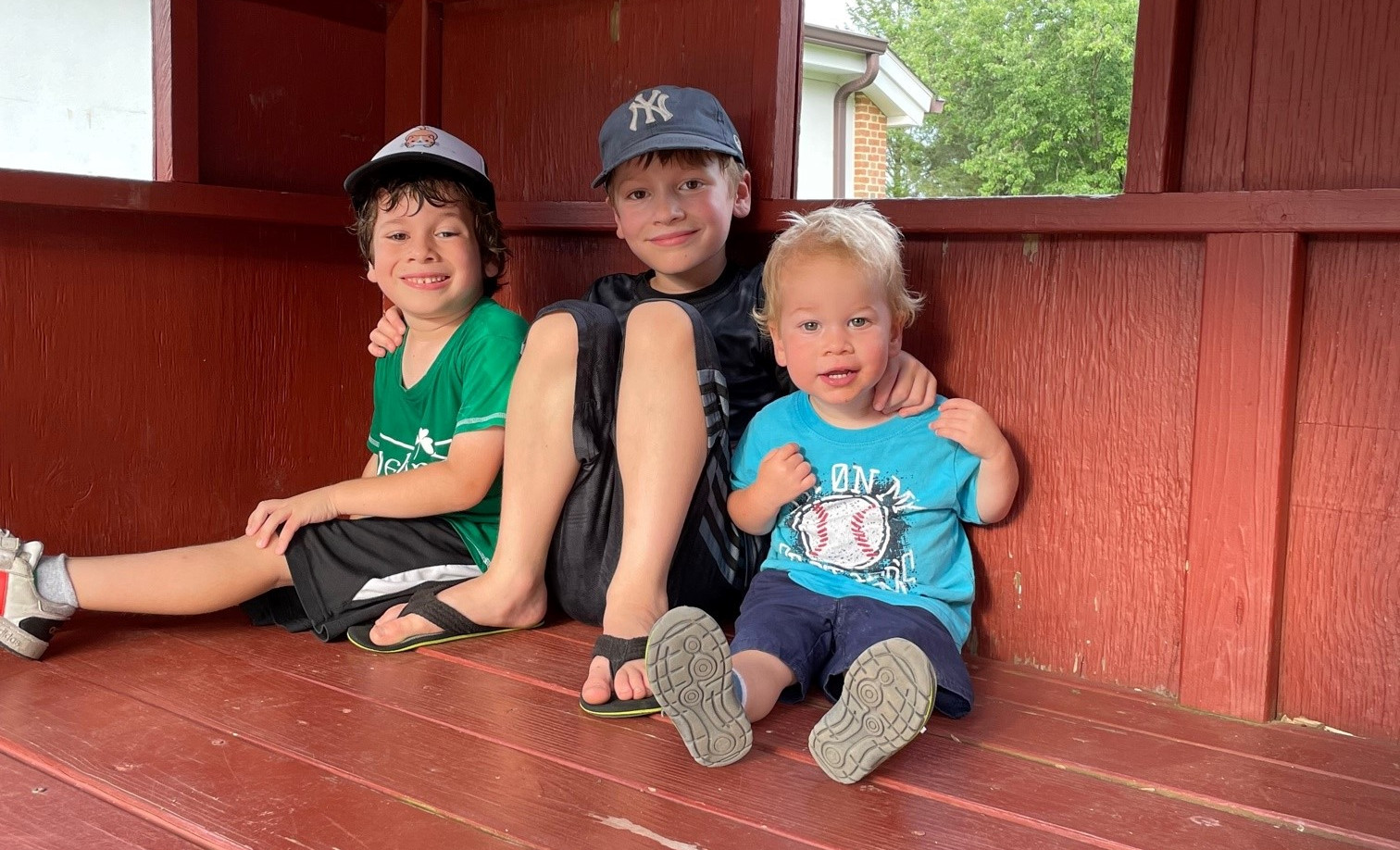
At Nipro, “Live Longer. Live Better.” is our mantra. Patients are at the core of all that we do, and this includes in the production of vials, ampoules, and glass tubings. The finished product when it leaves our plants is not the end of the cycle – we know and celebrate that the products will go on to be filled with life-changing drugs that will be used by real patients – this is what drives our perfection and desire to produce more and better. We make a direct and significant impact on patients by supplying the essential vessels.
In 2020, all of us at Nipro experienced almost first-hand the impact that our vials have on patients. An American colleague working for Nipro Pharmapackaging International, Ryan Matty - a sales development manager at our Millville branch, and his wife welcomed their baby boy, Noah Thomas Matty, to this world. As is the norm in Pennsylvania where Noah was born, mothers of newborns typically receive a TDAP vaccine which protects against tetanus, diphtheria, and whooping cough. The vaccine is administered to the mother, but the benefits of the vaccine are also transferred to the baby through breastmilk – thus protecting both the mother and child.

Ryan had been very supportive and involved in the whole labor process, and when he saw that a vaccine was about to be administered, started asking questions about the vaccine and of course, the vial that contained the vaccine
In Ryan’s own words:
“I was simply curious to see if this product had any connection to Nipro - turns out it did! Based on who the vaccine manufacturer was and the way the vial looked, I figured that it could very well have been produced by Nipro. The nurse was happy to give me the single-use vial after injection, knowing there was little risk to do so. The lot number was clearly printed on the vial. I asked my contact at the location of the pharmaceutical company whose product was in the vial if the vial’s lot number corresponded to or could be traced back to a Nipro vial. If so, it could likely be determined where and when the vial was manufactured. As it turned out, the vial was manufactured at our Nipro plant in Westport! I was surprised and proud that the vial containing the vaccine that was protecting my wife and son was from Nipro.”
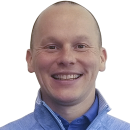
Furthermore, Ryan himself is a shining example of the people who work at Nipro. He genuinely wants the best for all customers, building trust and Nipro’s reputation in the industry.
He adds:
“Knowing first-hand that our vials have very specific purposes and every single one needs to be represented and made with the most care and quality, I try to act as a consultant and point of contact for my customers to ensure they’re getting exactly what they need, and not just pushing a product to meet a sales quota. I want customers to know that when they need support, they know who to come to (me or anyone else at our organization) and they will get the best level of service and quality product available to them.”
Indeed, it is with great pride today that Nipro can proudly say that we have witnessed the positive impact of our products on the lives of two of our very own. We remain committed to enabling patient safety through all our products, and our unwavering dedication to produce the highest quality of products will continue.